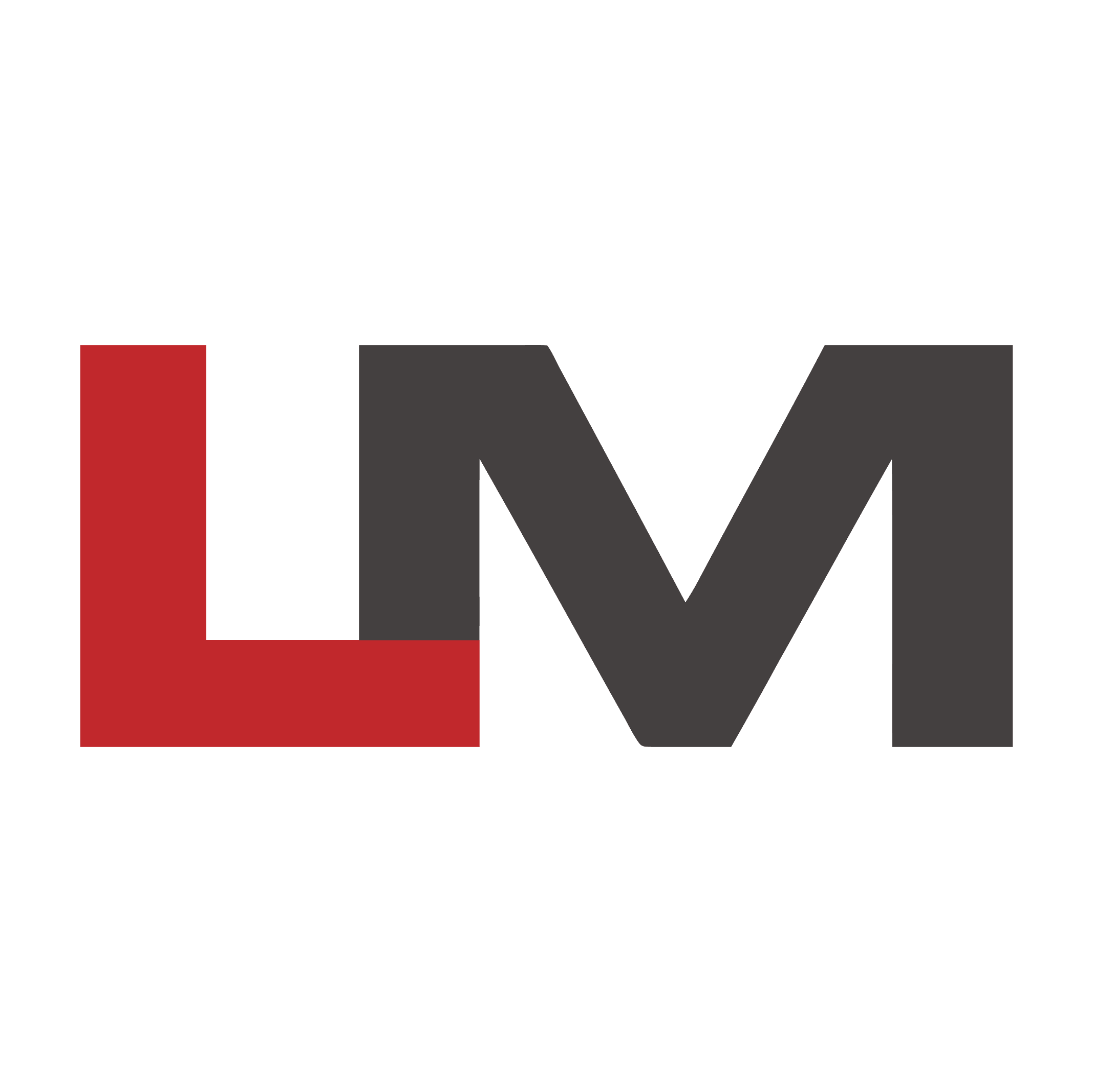
The system should be inspected and cared for properly before operation begins. Typical inspection includes confirming correct supply spool loading, web path, checking air pressure, ensuring rollers are clean and free of adhesive, checking pinch assembly operation, and label feed position. Do not attempt to operate system if not in good working order.
Preventative maintenance procedures should be performed at least once per week. This includes removing adhesive and residual build-up from system components, cleaning the label sensor, cleaning the tamp pad, and cleaning the pinch rollers.
To clean adhesive or residual build-up off of guide rollers, brake arms, or the pinch roller assemblies, use only isopropyl alcohol. Other chemicals or abrasive products can cause damage to the system, resulting in poor operation. Do not use sharp objects or aggressive solvents on the pinch roller assemblies to remove labels or adhesive!
Use clean, dry, compressed air to remove dust, dirt, or label debris from the label sensor, if applicable. Do not use any abrasive objects to clean the sensor slot, as it will cause unrepairable damage to the sensor.
The tamp pad should be cleaned with isopropyl alcohol to remove adhesive or debris build-up. The pad must be clean and smooth for the labels to feed properly. If adhesive is blocking any vacuum holes, use isopropyl alcohol to break down the adhesives and clean the holes. Do not use sharp objects or aggressive solvents on the tamp pad assembly to remove labels or adhesive!