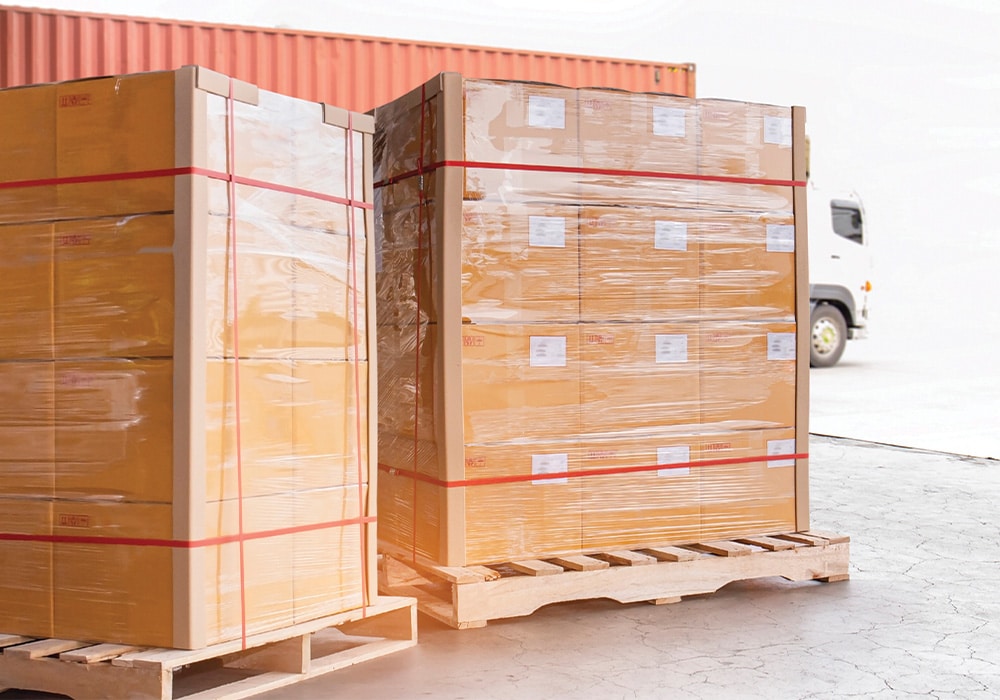
Our versatile pallet labeling system offers a wide range of options to accommodate various pallet loads, whether smooth or uneven surfaces, and applies labels to one side or all four sides with precision and efficiency. our solution ensures consistent label adherence without compromising accuracy.
Don't see what you're looking for?
Contact Us to Inquire about our Custom Options
Let's Talk about your Labeling Needs