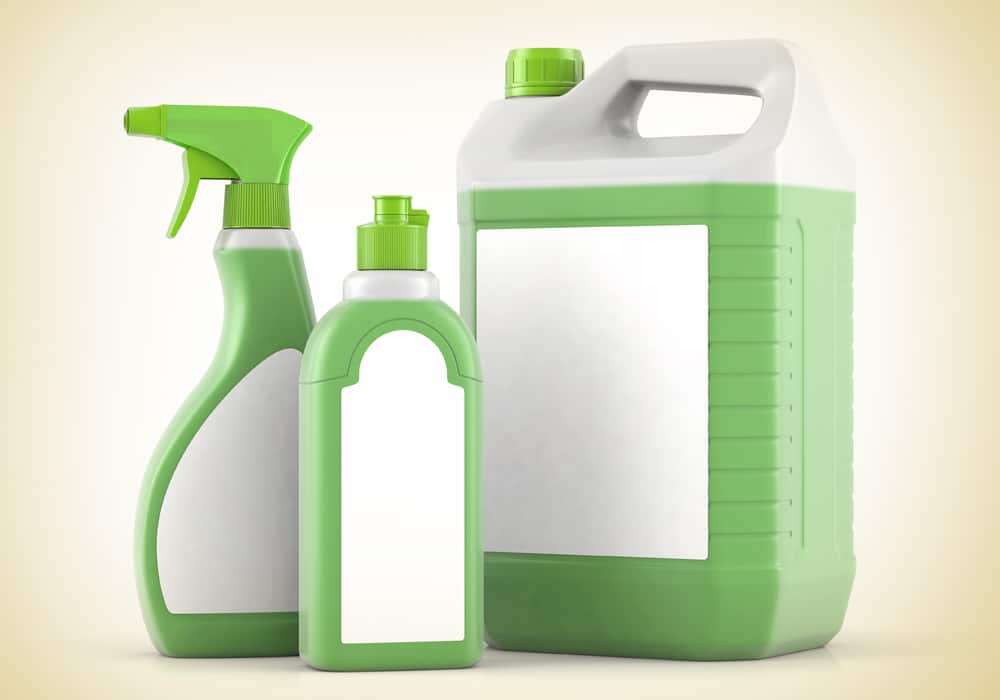
At LabelMill, we understand the importance of efficiency, precision, and quality when it comes to labeling your bottles. Discover the perfect finishing touch for your bottles with our diverse range of bottle label applicators. Craft brewers, pharmaceuticals, and many industries rely on our high standard label applicators
Don't see what you're looking for?
Contact Us to Inquire about our Custom Options
Let's Talk about your Labeling Needs